Understanding Asset Registers in Asset Management.
This article explores the crucial role of asset registers for a typical industrial organisation and its asset management system.
Asset registers serve as the foundational element of organizational asset management, they provide us with a systematic way of tracking, maintaining, and optimising physical and intangible assets.
I’ll explain how asset registers support critical business functions including financial management, maintenance planning, regulatory compliance and strategic decision-making.
I will also demonstrate how effective asset register implementation enables organizations to reduce unplanned downtime, optimise resource allocation, ensure regulatory compliance and make data-driven decisions.
There are detailed insights into the structure and functionality of asset registers, including equipment hierarchies, core components, and implementation strategies.
Special attention is given to practical applications, with a few examples and detailed specifications for asset documentation.
Key benefits highlighted include enhanced operational efficiency, improved maintenance actions, better financial control and effective risk management.
This article will hopefully serves as both a theoretical framework and practical guide for organizations looking to implement or improve their asset management systems.
Table of Contents.
1.0 Introduction to Asset Registers.
1.1. Financial Management.
1.2. Maintenance Management.
1.3. Compliance and Regulatory Requirements.
1.4. Risk Management.
1.5. Resource Planning.
1.6. Performance and Reliability.
1.7. Strategic Planning.
1.8. Data-Driven Decision Making.
1.9. Work Order Management.
1.10. Preventive Maintenance.
1.11. Spare Parts Management.
1.12. Cost Control.
1.13. Asset Register Details.
2.0 Core Components of an Asset Register
· Asset ID Management.
· Asset Core Business Management.
· Asset Lifecycle Management.
· Asset Register Advanced Functions.
· Asset Materials Management.
· Asset Register Review System.
· Specialized Review Functions.
· Reporting Capabilities.
3.0 Understanding Equipment Hierarchies.
· Top Level (Facility Level).
· Operational Units Level.
· System Level.
· Equipment Level.
· Component Level.
· Real-Life Benefits.
4.0 Implementing an Asset Register.
1. System Setup.
2. Configure Asset Hierarchies.
3. Set Up Tagging System.
4. Data Management.
5. Initial Data Collection.
6. Data Quality Controls.
7. Process Integration.
8. Staff Training.
9. Ongoing Maintenance Procedures.
10. Best Practices.
1.0 Introduction to Asset Registers.

An asset register is a crucial component of asset management, serving as a comprehensive inventory management system for organizations.
Essentially, it is a detailed record that catalogues all assets owned by an organization, for the most part, this relates to tangible items like equipment, machinery and vehicles and it can I extend to intangible assets such as intellectual property and software.
The primary purpose of an asset register is to maintain accurate and up-to-date information about these assets, which facilitates better decision-making and resource allocation.
An asset in an asset register is the cornerstone an industrial operation for a plethora of reasons, below is some of them:
1.1 Financial Management.
1. Enables accurate depreciation tracking
2. Supports capital expenditure planning
3. Provides clear insurance valuations
4. Helps track total cost of ownership
5. Facilitates ROI calculations
1.2 Maintenance Management.
1. Forms the foundation for preventive maintenance programs.
2. Enables tracking of maintenance history.
3. Supports spare parts inventory management.
4. Helps establish maintenance intervals.
5. Allows for condition monitoring.
6. Facilitates failure trend analysis.
1.3 Compliance and Regulatory Requirements.
1. Ensures adherence to safety standards.
2. Helps meet environmental regulations.
3. Supports audit requirements.
4. Maintains certification documentation.
5. Tracks regulatory inspections.
1.4 Risk Management.
1. Enables risk assessment and mitigation.
2. Supports criticality analysis.
3. Helps identify single points of failure.
4. Facilitates disaster recovery planning.
5. Supports insurance requirements.
1.5 Resource Planning.
1. Enables effective labour allocation.
2. Supports budget planning.
3. Helps optimise maintenance scheduling.
4. Facilitates contractor management.
5. Supports training requirements.
1.6 Performance and Reliability.
1. Enables performance tracking.
2. Supports reliability analysis.
3. Helps identify improvement opportunities.
4. Facilitates benchmark comparisons.
5. Supports efficiency optimisation.
1.7 Strategic Planning.
1. Informs replacement decisions.
2. Supports capacity planning.
3. Enables lifecycle management.
4. Helps with modernization planning.
5. Facilitates technology upgrades.
1.8 Data-Driven Decision Making.
1. Provides historical performance data.
2. Enables trend analysis.
3. Supports predictive maintenance.
4. Facilitates cost-benefit analysis.
5. Enables evidence-based decisions.
1.9 Work Order Management.
1. Creates a direct link between assets and maintenance activities.
2. Enables proper resource allocation.
3. Supports maintenance history tracking.
4. Facilitates maintenance planning and scheduling.
1.10 Preventive Maintenance.
1. Establishes maintenance intervals.
2. Defines maintenance procedures.
3. Tracks maintenance compliance.
4. Supports maintenance optimisation.
1.11 Spare Parts Management.
1. Links parts to specific assets via Bills Of Materials & Application Parts Listings.
2. Enables proper managed inventory levels (SKU’s).
3. Supports parts forecasting.
4. Allows your most critical assets (Tier 1) to have their related parts tagged as ‘business critical’ in the Spare Part/Material master data files.
5. Reduces downtime via avoiding parts availability issues.
1.12 Cost Control.
1. Tracks maintenance costs per asset.
2. Enables creation of quality budgets and future planning.
3. Supports cost-benefit analysis.
4. Facilitates lifecycle cost management.
Without a quality asset register, organizations would struggle with:
1. Unplanned downtime.
2. Inefficient maintenance.
3. Poor resource allocation.
4. Compliance issues.
5. Higher operating costs.
6. Suboptimal decision-making.
7. Inadequate risk management.
8. Poor financial planning.
An asset register is not just a list of equipment, it’s the foundation of modern asset management and directly impacts an organization’s bottom line through better maintenance practices, improved reliability, and optimised resource utilization.
Asset registers play a significant role in enhancing operational efficiency. They connect technical, financial, and operational aspects of the business, making it an indispensable tool for effective asset management.
By monitoring assets through their lifecycle, from acquisition to disposal, organizations can optimise their resource utilization and strengthen their financial management strategies.
Furthermore, a well-maintained asset register supports compliance with regulatory standards, ensuring that all assets are properly valued and accounted for in financial statements.
This level of transparency is particularly important during audits, as it reflects the organization’s commitment to governance and risk management.
Asset Registers provide system users with real-time access to information, enabling them to make informed choices regarding financial and maintenance strategies.
Hence, asset registers are not just functionality within your asset management software that identifies and tracks assets, they are a vital module of the larger framework of your asset management program.
1.13 Asset Register Details.
Below is an example of the type of information that can be captured for an industrial asset.
Asset Details | Details |
Asset ID | DOA100-005 |
Asset Site Location | Crushing Plant |
Asset Description | Crusher, Jaw |
Asset Category | Primary Crushing |
Work Execution Group | Mech01 |
Planning Discipline | MPL |
Production Area | Ore Preparation |
Production Process | Crushing & Sizing |
Cost Center | 20057880 |
Colloquial Tag | Jaw Crusher |
Superior Asset ID | PCP001 |
Asset Criticality | 1 |
Production Status | Current |
Last Modified By | D Vossey |
Last Modified Date | 10/10/2024 |
Create By | J Ventia |
Date Created | 01/01/2023 |
Alternate Reference Code | JC01 |
Date Purchased | 10/12/2022 |
Purchase Cost (AUD) | $1,002,852 |
Date Commissioned | 10/02/2023 |
Year/Month Of Construction | 20/11 |
Asset Owner Position | Mtce Mgr |
Cost Authorization Position/Workflow | AM2 |
Total Weight (Kg) | 135.000 |
Manufacturer | DAVOE |
Model Number | DV0001 |
Serial Number | DVJC0001 |
Dimensions | 5,300 mm x 4,000 mm x 4,700 mm |
Transport Instructions Exist | Yes |
Special Handing Instructions Exist | Yes |
Construction Material Specification | UNS S32750 |
Operating Capacity (TPH) | 1,500 |
Operation Redundancy | Yes |
Warranty Start Date | 10/02/2023 |
Warranty Expire Date | 10/02/2025 |
Pre Warranty Expiration Inspection Required? | Yes |
Purchased From | CMMS Success |
Lifecycle (Years) | 10 |
Rebuild Frequency (Years) | 5 |
Datasheet Exists | Yes |
Supplier Name | CMMS Success |
Asset Part Number (Supplier) | CMMS001 |
Asset Part Number Manufacturer | CS0001 |
Bill Of Materials Exists | Yes |
Bill Of Materials ID | BCS001 |
Asset Site | Muswellbrook |
Asset Site State/Territory | NSW |
Asset Location GPS Tracking | Yes |
In a nutshell, the more detailed we are with our asset information, the more beneficial the data will be for enabling effective asset management.
Be sure to include unique identifiers, operational insights, and financial data such as purchase cost and lifecycle planning.
The asset register data can outline maintenance requirements, warranty information, and compliance documentation to ensure that the asset is well-tracked and maintained.
Technical specifications, including dimensions and capacity, enhance understanding of the asset’s performance capabilities & overall footprint.
A comprehensive asset register supports efficient operations, safety protocols and informed decision-making in asset management.
2.0 Core Components of an Asset Register.
Below is an outline of the structure and functionalities of an Asset Register.
Many applications of a CMMS/asset management system are related to the core business purpose of an asset.
Identification of all assets is therefore vital to any such system and this is the role of the Asset Register.
In addition to its basic function of identification, the Asset Register should allow assets to be grouped together as a production group or process system.
Production groupings should be hierarchical and there should be no restriction on the number of levels.
A good Asset Register will have a large number of menu options to allow users to execute queries and reports or interrogate asset data from the one spot.
1. Asset ID Management:
1. Asset Identification Code.
2. Asset Description.
3. Asset Type.
4. Asset Structure.
5. Asset Classification.
6. Asset Tracing.
2. Asset Core Business Management:
1. Asset Core Function Description.
2. Asset Parent.
3. Asset Parent Core Function.
4. Asset Group.
5. Asset Group Report.
6. Asset Maintenance Strategy.
7. Asset Criticality Classification.
8. Asset Integrity Review Frequency.
9. Access Asset Budget Information.
10. Review Current Work Requests.
11. Create A Work Request.
12. Review Work Order History.
13. Statutory & Regulatory Compliance Actions.
14. Health, Safety, Environment & Community Actions.
3. Asset Lifecycle Management:
1. Temporary Deactivation Of Asset (Mothballing).
2. Temporary Deactivation Of Asset Group.
3. Retire/Decommission An Asset.
4. Retire/Decommission An Asset Group.
5. Restore Mothballed Asset.
6. Restore Mothballed Asset Group.
7. Recommission an Asset.
8. Recommission an Asset Group.
9. Asset Acquisition Data & Report.
10. Asset Commissioning Data & Report.
11. Asset Warranty Data & Report.
12. Asset Shutdown Management Profile.
13. Asset Disposal Management.
14. Asset Lifecycle Status Review.
3. Asset Register Advanced Functions:
1. Asset Classification Management
2. Asset Colloquial Names.
3. Asset Class Management.
4. Asset Alternate References Management.
5. Asset GPS Tracking Management.
6. Asset Profile Information Management.
7. Asset Operating Capacity & Statistics Profile.
8. Access Live Asset Data Dashboard (Yokagawa DCS/Citec)
9. Asset Downtime & Reliability Codes (DCS/Citec).
10. General Asset Profile.
11. Asset Costing Rates.
12. Asset Dimensions Data.
5. Asset Materials Management:
1. Review Bill Of Materials.
2. Update Bill Of Materials.
3. Link Asset To Material Number.
4. LinkOne Access.
5. Asset Register Review System:
1. General Review Functions.
2. Asset Register Inquiries.
3. General Asset Information Review.
4. Classification Information Review.
5. Colloquial Names Review.
6. Specialized Review Functions:
1. Disposal Information Review.
2. Asset Search by Description, Status and Classification.
3. Asset Costing & Budgeting Review.
4. Maintenance Strategy Review.
5. Asset Tracing Information Review.
7. Reporting Capabilities.
1. Master Asset Register (Detailed and Summary versions).
2. Asset Register Integration Links.
3. Search Assets By Manufacturer’s Name.
4. Search by model number.
5. Search by Asset Location.
6. Find Asset Current GPS Location.
7. Asset GPS History.
8. Asset Budget Reports.
9. Create Maintenance Systems Audit Report.
10. Maintenance Systems Audit History.
An asset register serves as a centralized repository, collecting and organizing crucial information about an organization’s assets.
The core components of an asset register include detailed asset descriptions, specifications, unique identifiers, physical locations, acquisition dates, costs, warranty information, and maintenance records, among others.
Each of these elements plays a significant role in the effectiveness of asset management.
Asset description data provides fundamental information, including the type and nature of each asset, which allows for quick identification and categorization.
Specifications further enhance clarity by detailing attributes such as model numbers, dimensions, and capacities, ensuring stakeholders have access to relevant technical data.
Unique identifiers, often in the form of serial numbers or barcodes, enable efficient tracking and retrieval of information associated with each asset, thus mitigating the risk of misplacement or duplication.
Accurate physical location data of Assets within an organization, whether they are operating zones, production levels, geographical areas, GPS coordinates or within an office, are essential for effectively managing asset maintenance actions.
No tradesperson wants to spend too much time tracking down an asset that has malfunctioned, nor should an organisation want that to even be a factor.
By documenting where assets are situated and keeping that information up-to-date, organizations can streamline asset management and best optimise resources.
The acquisition, commissioning and warranty start dates are other critical pieces of information that aid in understanding the asset’s lifecycle and helps people to make informed decisions regarding warranty claims, depreciation as well as mid-life rebuild and replacement planning.
Cost records will provide financial insights, allowing organizations to evaluate the return on investment for their assets.
There should be access to the Asset Budget Information from the Asset Register, whether it be to update a budget or run reports on Planned Versus Actual budget costs.
The Asset Register should allow users to access maintenance data for a few core reasons:
1. Review current work requests.
2. Create A work request.
3. Review work order history.
The easier an Asset Register makes it for people to find assets, the quicker people can be reporting defects via a work request.
Asset registers play a vital role in financial control. They provide accurate data on asset valuation, depreciation, and lifecycle costs, allowing organizations to establish precise budgets and financial forecasts.
The insights drawn from an asset register can enhance the allocation of financial resources, ensuring that funding is directed towards critical asset needs while highlighting the need to inspect and make important decisions on under-performing assets.
It’s important that the Asset Register provide users with access to Lifecycle Management Actions for an Asset such as taking an asset out of service or restoring a retired asset, for example:
· In the oil and gas industry, wells or platforms may be temporarily decommissioned and later recommissioned if oil prices rise significantly.
· Power plants might be recommissioned to meet unexpected energy demands or after retrofitting with new technologies.
Operational Status is another significant benefit derived from implementing a quality asset register.
By tracking the status and condition of assets, organizations can streamline maintenance, thereby reducing downtime and increasing productivity.
A comprehensive asset register helps to ensure that maintenance activities are executed timely.
Compliance reporting is also an essential function of an asset register.
With stringent regulations governing asset management in various industries such as Oil & Gas, Mining & Aviation, asset registers assist organizations in ensuring compliance.
This is enabled by providing a clear and accurate inventory of all assets as well as dedicated functionality to manage compliance data.
This transparency enables easier audits and promotes accountability, ultimately reducing the risk of non-compliance penalties.
Additionally, asset registers can be invaluable in support of safety and sustainability initiatives, helping organizations manage an assets safety, environmental & community impacts.
3.0 Understanding Asset Hierarchies.

Asset hierarchies are fundamental structures used in asset management to organize and categorize various assets systematically.
By creating a defined multi tier hierarchy, organizations can effectively manage their assets, leading to improved oversight, accountability, and operational efficiency.
At the top level of the hierarchy, we find the facility or site level, which serves as the highest aggregation point for all assets within a particular location. This overarching classification enables a centralized approach to asset management, ensuring that all assets within the site are identified and managed.
Below the facility level, the hierarchy typically breaks down into groups based on operational units, production processes or departments.
Each grouping may encompass specific asset categories, such as production equipment, fleet vehicles, or maintenance equipment.
This subdivision allows for precise tracking and management of assets relevant to particular functions, facilitating maintenance activities, performance evaluations, and operational reporting.
Recognizing the relationships between assets at a particular hierarchical level aids in optimising utilization and ensuring those assets are meeting performance expectations.
Further down the hierarchy, one can identify the individual assets and their components, including spare parts.
This granular level of organization is critical, as it enables organizations to maintain accurate inventories and ensure the availability of necessary components when required.
Below is a breakdown of an example of this:
1.0 Top Level (Facility Level): A vehicle manufacturer.
2.0 Operational Units Level:
2.1 Production Area: Where actual manufacturing happens.
2.2 Warehouse: Where materials and finished products are stored.
2.3 Maintenance Workshop: Where equipment repairs take place.
3.0 System Level:
3.1 Assembly Line 1: A specific production line.
3.2 Forklift Fleet: Transportation equipment.
3.3 Quality Control: Testing and inspection equipment.
4.0 Equipment Level:
4.1 Robotic Welder.
4.2 Conveyor System.
4.3 Individual Forklifts.
5.0 Component Level:
5.1 Welding Robot Parts.
5.2 Control Systems.
5.3 Power Units.
Real-Life Benefits:
Maintenance Actions:
· If a robotic welder breaks down, maintenance teams can quickly locate it within the hierarchy
· They can see which assembly line it affects and prioritise repairs based on production impact.
Cost Tracking:
· Management can track maintenance costs at any level.
· Example: Compare maintenance costs between Assembly Line 1 and 2, or between different facilities.
Performance Monitoring:
· Track efficiency of specific equipment.
· Example: Monitor the performance of individual forklifts to plan replacements.
Resource Allocation:
· Understand which areas need more maintenance attention.
· Plan preventive maintenance actions efficiently.
Decision Making:
· Make informed decisions about equipment upgrades.
· Identify problematic areas through historical data.
· Plan capital expenditure based on equipment performance.
Hierarchical asset structures help organizations:
· Keep track of thousands of assets.
· Plan maintenance efficiently.
· Allocate resources effectively.
· Make data-driven decisions about equipment lifecycle.
· Maintain compliance with regulatory requirements.
Think of it like a family tree for assets, where understanding the relationships helps manage everything more effectively.
Each level provides different insights and control points for managing the assets. By implementing an effective asset hierarchy, organizations can streamline asset management processes.
This ensures better planning, scheduling and execution of maintenance and minimizes disruption to operational activities.
Establishing a clear framework for asset organization provides a foundation that enhances overall asset management practices, fostering a culture of efficiency and accountability across the organization.
4.0 Implementing An Asset Register.
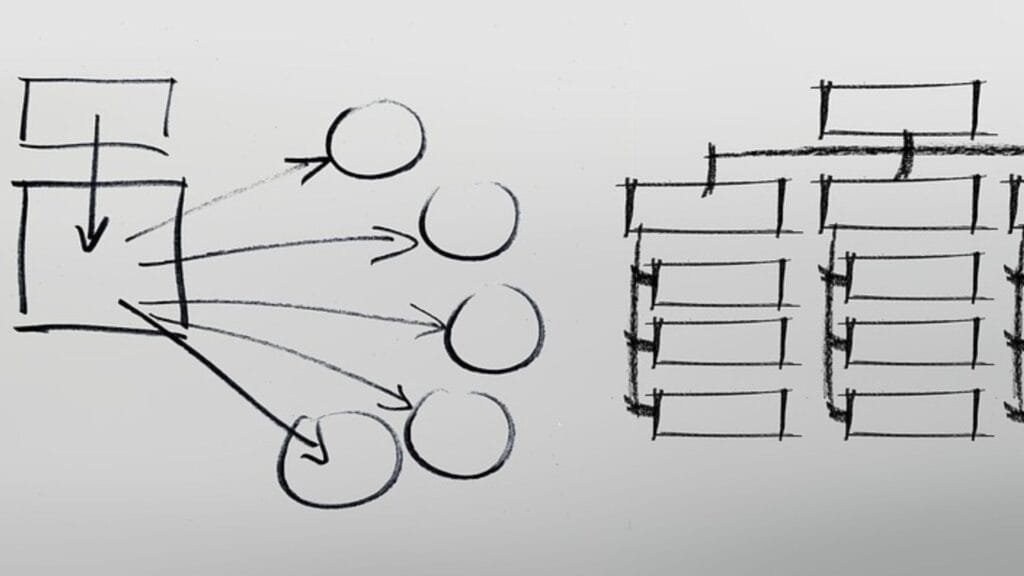
Implementing a quality asset register is a critical step in effective asset management.
A well-implemented and comprehensive asset register provides organizations with accurate, up-to-date information about their assets, enabling better decision-making, improved operational efficiency and enhanced financial control.
Below is a guide to implementing an asset register:
1.0 System Setup – Choose the Right Software.
Selecting appropriate asset management software is crucial for successful implementation, so consider the following factors:
1.1 Scalability to accommodate future growth.
1.2 User-friendly interface for easy adoption.
1.3 Customisation options to fit specific organizational needs.
1.4 Integration capabilities with existing systems.
1.5 Robust reporting and analytics features.
2.0 Configure Asset Hierarchies.
Establish a logical structure for categorizing assets, this may include:
2.1 Asset classes (e.g., IT equipment, vehicles, machinery).
2.2 Locations or departments.
2.3 Functional groups.
3.0 Set Up Tagging System.
Implement a consistent asset tagging system3. Options include:
3.1 Barcodes.
3.2 QR codes.
3.3 RFID tags.
3.4 GPS trackers.
4.0 Data Management – Establish Data Standards
Create standardized protocols for data entry to ensure consistency and accuracy and this should cover:
4.1 Naming conventions.
4.2 Required fields.
4.3 Data formats.
5.0 Conduct Initial Data Collection.
Perform a thorough audit of existing assets, this process should:
5.1 Identify all relevant assets.
5.2 Collect required information (e.g., make, model, serial number, purchase data).
5.3 Verify asset conditions.
6.0 Implement Data Quality Controls.
Set up mechanisms to maintain data integrity:
6.1 Regular data audits.
6.2 Automated data validation rules.
6.3 User access controls.
7.0 Process Integration – Align with Existing Workflows.
Integrate the asset register with current business processes and this may involve:
7.1 Updating procurement procedures to include asset registration.
7.2 Incorporating asset tracking into maintenance schedules.
7.3 Linking the asset register to financial reporting systems.
8.0 Train Staff
Provide comprehensive training to all relevant personnel and the training should cover:
8.1 System usage.
8.2 Data entry procedures.
8.3 Reporting capabilities.
9.0 Establish Ongoing Maintenance Procedures
Develop processes for keeping the asset register up-to-date:
9.1 Regular physical audits.
9.2 Procedures for recording asset acquisitions and disposals.
9.3 Periodic data reviews and updates.
10.0 Best Practices.
To ensure successful implementation and ongoing effectiveness of the asset register:
10.1 Set Clear Objectives: Define specific goals for the asset register implementation, such as improving asset utilization or reducing maintenance costs.
10.2 Engage Stakeholders: Involve key personnel from various departments to ensure the asset register meets diverse organizational needs.
10.3 Start Small: Begin with a pilot project or focus on a specific asset category before full-scale implementation.
10.4 Leverage Automation: Utilize automated data collection methods where possible to improve accuracy and efficiency.
10.5 Conduct Regular Reviews: Schedule periodic assessments of the asset register’s effectiveness and make necessary adjustments.
10.6 Ensure Data Security: Implement robust security measures to protect sensitive asset information.
By following these guidelines, organizations can implement a comprehensive and effective asset register that supports improved asset management, financial control, and operational efficiency.
In conclusion, asset registers have evolved from simple inventory lists into sophisticated management tools that form the backbone of modern industrial operations, enabling organizations to make data-driven decisions, optimise resource utilization, and maintain regulatory compliance.
Through proper implementation and maintenance of an asset register, organizations can significantly reduce operational costs, minimize downtime, and extend asset lifecycles while ensuring optimal performance and reliability of their equipment.
A well-structured asset register becomes not just a operational necessity but a strategic advantage, providing the foundation for predictive maintenance, intelligent resource allocation, and sustainable asset management practices.