Important tips for those people thinking about planning a Shutdown
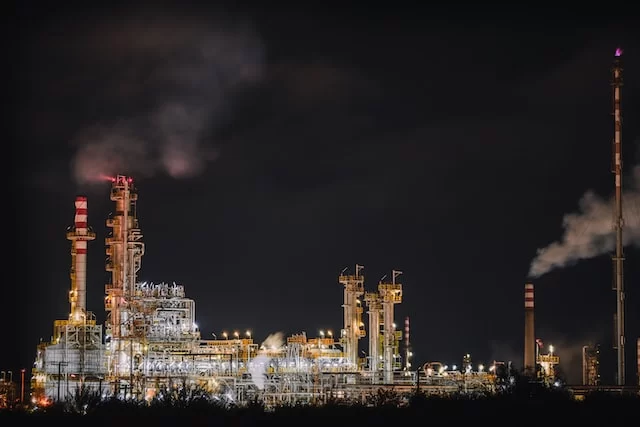
Note: This article should be read in conjunction with Maintenance Systems Audit Part 2 – Module 5 – Execution Readiness.
More than simply checking off tasks, successful shutdown management requires the thoughtful application of sound principles. The principles of shutdown management are typically learned through experience, but they can definitely be taught since they are not greatly dissimilar from those of standard project management.
The designated shutdown manager is responsible for ensuring that any principles and guidelines are carefully followed during the planning and execution of the shutdown. Additionally, the shutdown manager must ensure that each member of the shutdown leadership team is aware of what falls within and outside of their purview.
Indeed, the most important aspect of shutdown management is ensuring that everyone knows what they are supposed to be doing and when they need to do it by, and then just being attentive. A lot of the time you are looking for anyone in the team that is struggling and making sure they get the support required.
The scope of work is the most important aspect of the shutdown strategy. Incorrect or lacking definitions of what is actually required will almost certainly result in schedule delays, wasted resources, and dissatisfaction among the senior management team.
Task-by-task scope review and analysis should begin as soon as possible, and the business/production requirements and event expectations should be handed over to the shutdown planning team concurrently.
All event-related data will be scrutinised for anything that could increase costs or take too long, endangering the success of the event. The senior management team may require some requirements to be negotiated down, modified, or sometimes increased in scope due to current production difficulties.
As there will be different outage durations for some of the areas, which are likely related to how the plant is shut down and restarted for an outage event, the shutdown event requirements analysis should quickly become specific to each production area of the plant. A team of maintenance, engineering, and production personnel must perform a thorough and in-depth analysis of each process area while factoring in the needs and concerns of all project stakeholders.
When reviewing hundreds of tasks, it is all too easy to gloss over some details and omit necessary clarity, as well as fail to identify underlying problems and potential conflicts. Before making any major commitments, the production leadership team should review and approve the completed requirements analysis of a shutdown event, as they and their team members are the ones who know the plant the best.
On large shutdowns, the first major meeting is frequently the final pass of a requirements review, and this is where the wheat is separated from the chaff. Following the first major meeting, a clear statement of shutdown objectives will be issued. Wants and needs will be distinguished and separated as the team conducts a thorough and comprehensive analysis. The outcomes of this meeting will be clearly documented, and all actions identified will be assigned to individuals and a completion date/time.
The next step is to determine whether any businesses similar to yours plan to have a major outage event at the same time as you. If this is the case, it is possible that some critical resources you will almost certainly require have already been reserved for another company. You may be fortunate in that this other company only made a tentative booking. They may not have begun the event planning process yet and, as a result, have not committed to shutdown start/finish times. If this is the case, you may be pleasantly surprised at how accommodating they are to your needs.
Creating the shutdown project plan provides a structured framework for thinking about how the project will be carried out, which is critical for considering project risks. A comprehensive shutdown plan will necessitate the participation of a wide range of subject matter experts, as well as multiple decision-makers.
The process, rather than the outcome, is a significant benefit of getting to the point where you have a very thorough and well-regarded shutdown plan. Shutdown planning forces people to consider the best possible approach for getting a job done while also considering the needs of others, avoiding scheduling conflicts, and fleshing out key decision points.
You won’t be able to get a shutdown plan approved unless you show that your team is willing to make commitments to ensure the event’s success, which can be both a difficult and important part of getting the shutdown approved.
The project plan provides a vehicle to facilitate executive and customer review. It should make major assumptions explicit and provide a forum for communicating the planned approach and for obtaining appropriate approvals.
To ensure that there are no ambiguous lines of authority and communication, it may be useful to write a Shutdown Management Plan that describes the roles and responsibilities of the various organisational participants. It can also be used to communicate management systems and procedures that will be used throughout the planning and execution of the shutdown.
If the planned shutdown event appears to be challenging in a few areas, it is critical to lock and control the scope as soon as possible. This will free up more time for micro-scheduling of more complex and risky tasks/projects. This should also help to keep the costs of the more difficult aspects of the shutdown in check.
It may still be possible to include a task in the shutdown after the scope has been locked, but there will be a ‘scope break in’ process that must be reviewed and approved using a risk-based approach, and approval of shutdown break in tasks may be at the general manager level and they will require sign off from all business sections prior to making a decision.
Effective shutdown management can be achieved only when thorough planning, materials management, cost controlling, scheduling, and operations objectives are clearly outlined, realistically organised, and safely managed.
The shutdown planning process should result in all stakeholders having a clear understanding of the what, when, where, how, and who questions as they relate to the event.
Finally, I believe that the general manager or higher should communicate to managers outside the shutdown management team that they must refrain from interfering with approved shutdown events during the execution phase. Although these individuals may have good intentions, if they are able to introduce unapproved tasks into the execution phase, they may unintentionally increase shutdown risks, resulting in an injury or a delay in the start-up sequence. I believe these individuals realise that if they approach the shutdown manager directly during these events, they will be quickly dismissed, so they try to avoid that situation by directing their needs to people lower in the shutdown hierarchy.
Shutdown team members on the receiving end of such situations should simply thank the individual for their contribution and say they will run their idea up the flagpole to see what the shutdown manager says. It may seem difficult to imagine that any manager might attempt to interfere with the safe and timely completion of a shutdown, but it happens more frequently than you might think.