Complete Maintenance Systems Audit - Part 1
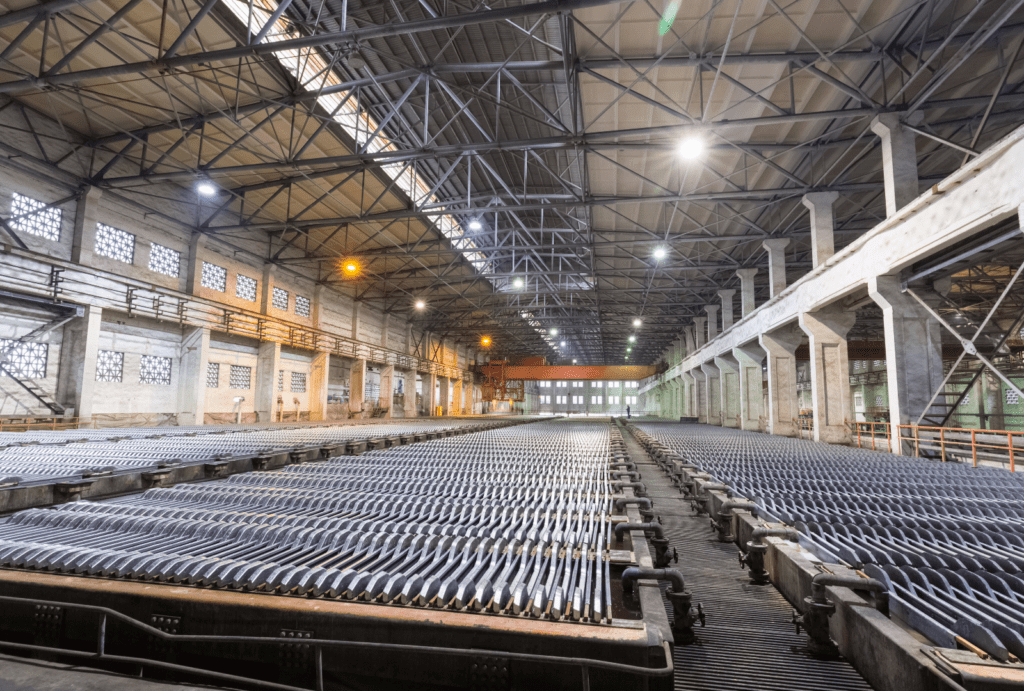
There are many good reasons for carrying out periodic maintenance management systems audits in the following modules as follows:
Maintenance Department Performance Measurement
1. Create a baseline against which future maintenance improvement actions and projects will be measured.
2. By auditing the same criteria in 12 or 24 months time, you will be able to determine what is working and what isn’t.
3. Understanding maintenance management system behaviours
Common symptoms for needing a maintenance systems audit

1. You are not performing well in certain areas and you do not understand why.
2. You appear to be dealing with standard tasks well at times, but why not consistently?
3. We try to do things properly when we have time.
4. Your leadership team appear to be stressed and look tired, they are non-stop attending meetings that seem to add no value and are hardly ever seen interacting with their staff.
5. Very few of your staff can remember the last time they did anything that wasn’t reactive. They don’t feel as though they would have time to help with any improvement initiatives.
Indicators that your maintenance department is performing well
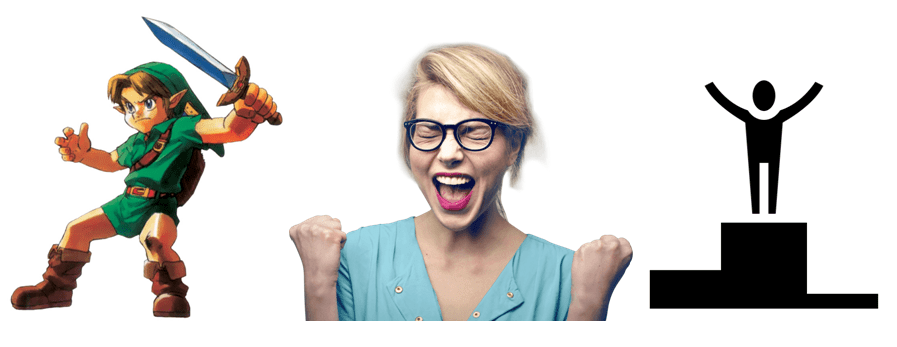
1. You are actively looking for problems within your workplace and management systems and dealing with them.
2. You don’t accept that any problems need to exist and you help each other with the tools & skills required to keep everything in top shape.
3. Your leadership team has clearly adopted the company’s core values and is driving continuous improvement at all levels of the organisation.
4. Employees have been assigned specific times each week to work on improvement projects, either as a team or on individual projects, as part of their six-month evaluation process.
Top 10 recommended Maintenance Systems Audit Modules
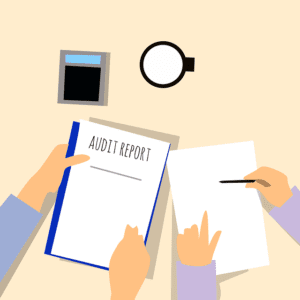
1) Master Data & Maintenance Strategy Development
2) Identify Work
3) Plan Work
4) Schedule Work
5) Execute Work Readiness
6) Execute Work
7) Complete Work
8) Maintenance Systems Management & Compliance
9) Improvements
10) Managing Costs & Reporting Functions
General Information about the Maintenance Systems Audit Process
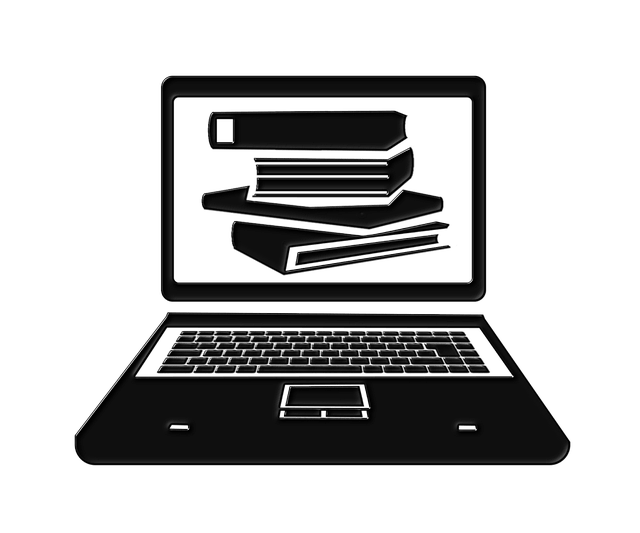
1. Data is to be gathered via interviews, observations, analysis and other methods that may be required to ensure the audit is effective.
2. You will need to develop a percentage scale for how well your business is performing in relation to a particular question.
3. For the questions where a percentage of achievement is relevant, below is a suggested scale:
· 0 = <50%,
· 1 = 50% to 75%,
· 2 = >75%
4. For the questions where the answer is that they have either achieved the result, not achieved the result or partially achieved the result, below is a suggested scale:
· 0 = No
· 1 = Partial
· 2 = Yes
Maintenance Systems Audit Module 1 – Master Data
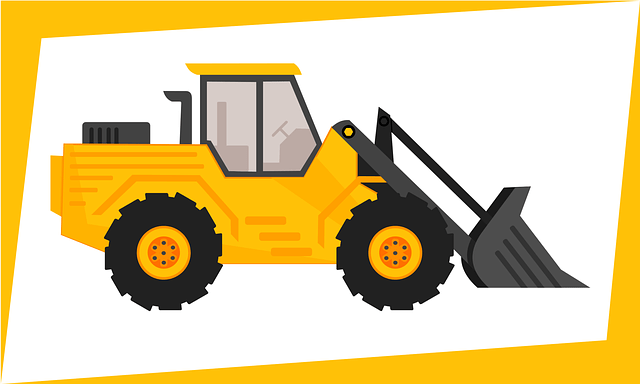
This section assesses if your business is managing to:
1. Capture all the data of the equipment purchased and commissioned at your organisation within the CMMS
2. Develop maintenance strategies for all maintainable assets.
Evidence should show that:
1. Master Data creation is a part of the project plan for commissioning new equipment.
2. Master Data creation for new equipment is being performed using capital cost centres assigned for the project.
3. All types of equipment audits (Safety & Operational Readiness) are being performed on all new equipment prior to use.
2 Yearly physical plant audits
To ensure that your physical assets matches the assets listed in the equipment register of your CMMS, a physical plant audit should be conducted every 2 years maximum.
Unfortunately, project teams can sometimes fail to include getting the master data for newly commissioned assets as part of their scope.
Creation of newly commissioned assets.
If the equipment has not been created, then there will be no maintenance strategy, no work orders being created to rectify defects etc, which is potentially a very dangerous situation.
Deactivation or Retirement of decommissioned assets.
1. If the decommissioned equipment has not been deactivated within the CMMS, there may be active maintenance strategy based preventive tasks being automatically generated for no reason.
2. There may be instances where costs are incorrectly posted against assets that no longer exist at your company.
Maintenance Strategy Development
Maintenance strategies should be developed through the use of risk-based analysis. It is preferable to use FMECA analysis, but a score can be recorded as long as some form of failure mode based task and spares analysis has occurred and the results of this process have been entered into the CMMS.
Asset Hierarchy Data Quality
1. Is the asset hierarchy within the CMMS consistent, it appears as though a template is being utilised.
2. Does it appear as though there is a naming convention being used for identifying assets?
3. Are all critical equipment identified using an assessment process? Is this information readily accessible for all staff? Have the criticality rankings been entered into the CMMS? Does entering of a criticality designation against an asset prompt additional CMMS actions?
Materials Management
1. Have ‘Bills of Materials’ or ‘Asset Parts Listings’ been created for all critical equipment and entered into the CMMS? Is there evidence that this data is reviewed at least every 6 months? For instance, supplier part updates are being included, redundant or removed parts are being deleted from these lists.
2. Do Max/Min stock levels exist for Critical Parts? If not are there acceptable lead times for these ‘order on demand’ parts?
3. Do parts intensive preventive maintenance plans have parts listings included so that the CMMS is automatically processing these requirements sufficiently prior to the maintenance execution windows?
4. Are maintenance workers often required to obtain additional parts for preventive maintenance work orders? If so what % of parts is being added?
Maintenance Systems Audit Module 2 – Identify Work

This module is dedicated to understanding how new work is identified and whether it is effectively processed.
1. Is there a documented process for initiating new work? Have people seen it?
a. Do they understand it?
b. Is it being followed?
2. How do people without CMMS access alert the maintenance team about defects that need to be rectified?
a. Is there a work request form they can fill out?
b. Is the information from these forms entered into the CMMS as a work request?
3. Are all new work requests reviewed every 24hrs by a team?
a. This process needs to be conducted by more than 1 person
b. Is the work request originators priority designation reviewed & risk assessment process used to update?
c. Except for emergency work orders, are all work requests approved prior to the creation of work orders?
d. Is it possible for the CMMS to prevent unapproved work requests from being converted into work orders?
4. Are work requests reviewed for quality?
a. Periodic review of work requests to reveal the quality of information being entered by originators.
5. What is the level of duplication in the CMMS?
a. Are originators checking to see if there already is a work request for an approved work order for the problem?
i. If so, maybe the existing work order needs to be escalated in priority, is escalation possible?
ii. If the CMMS is not being checked for existing details there may be a situation of duplicate tasks.
b. Is the CMMS periodically checked for duplicate work?
6. Are separate work requests created for each problem?
a. Originators should not be creating work requests for multiple defects/problems.
b. One defect requires one work request.
7. What is the average time taken from work request creation to work order completion?
a. For the work orders that have not been completed within a reasonable time frame, are there comments or reason codes on the work order to explain the inaction?
Maintenance Systems Audit Module 3 – Plan Work

This module investigates:
a. The level of planning effort applied to work orders with the ‘fully planned’ designation (or similar).
b. The level of training, documentation support, and other software or processes made available to maintenance planners to ensure they have access to all available information.
1. How structured is the planning process?
a. Do the planners fully understand their expectations of their core role?
b. If maintainers identify corrections to be made to planned work orders, are there comments reviewed and processed?
c. Is there a standard or specification for what is a fully planned work order?
d. Is there a step by step procedure for planning a work order?
2. Standard Task Creation
a. Do maintenance planners create standard jobs or task lists for reoccurring corrective maintenance tasks?
b. If they do, how many a month on average do they create, you could search the CMMS looking for that type of data whereby the creator is that person’s username.
c. If not, do they know how to do it?
d. If they do know, what is the reason for not creating them?
e. If they don’t know, is there a procedure for creating a standard job/task list for such a task? If not, who is responsible for creating one?
3. Work Order Trade Resources
a. Are all the various resource/trade types identified separately on the work order tasks/operations/activities?
b. Are the numbers of these resources identified as well? Such as 2 x Tyre Fitters.
4. Are durations and total planned work hours identified for each task?
a. If so, how accurate have they been? Review last 12 months of data for a random selection of fully planned work orders and compare planned verus actual hours on work order tasks/operations/activities.
b. If not, how is the execution labour requirements planned for the next period? How is the execution team performance measured? How is capacity planning achieved when compiling the work schedule?
5. How is non-completed work handled?
a. Is there a process or guideline for how backlog work is managed?
b. On average, how long are maintenance planners leaving the non completed work orders with a start date that is in the past?
c. Is there an expectation, standard or specification from the company about maximum size and age of backlog work orders?
d. Does the leadership team ensure that work orders not completed during an approved execution period are reviewed, the reasons for non completion discussed, priority and scope challenged and possibly updated and the work order assigned a new planned start date?
6. Work Packs
a. Are work packs created for fully planned work orders?
b. A work pack might include P&ID’s, isometric drawings, general layout drawings, technical updates from the manufacturer, inspection and test plans, material specifications, heat treatment and related welding requirements, special safety instructions etc.
7. Work Order Content/Quality Feedback
a. Is there a documented procedure for the maintainers to mark-up corrections to work orders?
b. This is often referred to as ‘Red Pen Mark-ups’, meaning that if the maintainer has identified errors with the work order scope, durations, trade types, parts listings etc, the maintainer will make these corrections either adjacent to the original information in red pen or at the base of the work order printout where there are typically several lines provided for comments.
c. Do Supervisors review and approve Red Pen Mark-Up comments? Is the hardcopy of the work order that contains the Red Pen Mark-Ups scanned and then attached as a document to that work order so that this information is never lost?
d. Does the Maintenance Planner or Supervisor contact the originator of the Red Pen Mark-up comments to let them know the progress of their comments?
a. For instance, the maintainers Red Pen Mark-Up comments may not have been suitable or correct, in which case these comments were rejected.
b. Alternatively, the comments have been adopted by the company and changes are being made.
Maintenance Systems Audit Module 4 – Schedule Work
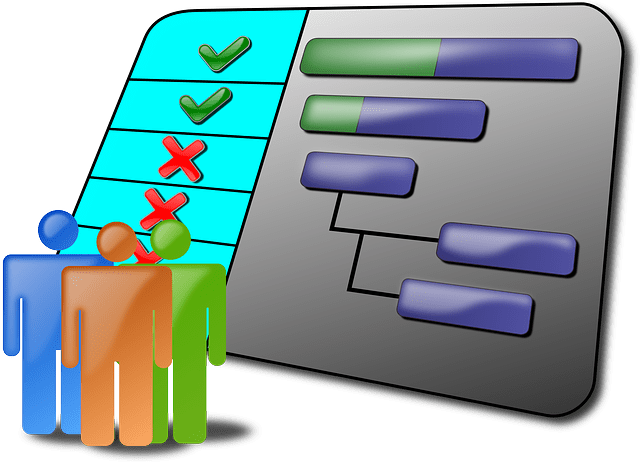
This module determines whether the maintenance group is committed to the scheduling process.
1. Are all stakeholders identified and involved in the scheduling process?
2. Do all stakeholders contribute information/data for review as part of the schedule review process?
3. Is there a set of criteria for determining whether a fully planned work order is approved for inclusion in the list of work orders to be reviewed for inclusion in the next schedule?
4. Is the schedule period greater than 1 week?
a. It is common practice that a scheduling period should now be at least 2 weeks into the future.
5. When scheduling meetings take place, do all stakeholders review maintenance, operations, warehousing, purchasing and contractor requirements?
6. Do all stakeholders contribute towards the schedule build?
a. If yes, make note of some examples, this will positively reinforce the scheduling process importance.
b. If not, do you feel as though people are just turning up to scheduling meetings and hoping to get through this process as soon as possible? Or is it because too many jobs that are obviously not fully planned have been included into the review process?
7. 12 Week Look ahead
a. Is it possible for the scheduler to look ahead at committed labour assignments per work group for at least 12 weeks?
b. If not, ask the maintenance manager to consider making this a priority.
8. If the footprint of this company is quite large (very large building) or is multi-site spaced over many kilometres and maintainers are required to travel extensively on a regular basis
a. Is there a ‘bundling’ of work orders to minimise waste via unnecessary travel?
i. If not:
1. Does the CMMS have the ability to group work orders by geographical location/GPS Coordinates?
2. Bring this issue up with the Maintenance Manager, there could be substantial savings to be had.
9. Meeting participant engagement
a. Do scheduling meeting attendees appear to have done any preparation?
b. Are they referring to any notes? Do attendees take notes?
c. Are they able to make any useful suggestions that could affect the schedule?
10. Are there 3 levels of scheduling meetings?
a. Rough Cut
b. Challenge and
c. Approval.
11. Scheduling Meeting Effectiveness
a. Are actions identified during the various levels of scheduling meetings assigned to individuals and dated for completion prior to the start date of the next meeting?
i. The reason for checking on this is so that the individual assigned an action will have time to inform the group of their actions/outcome.
b. Is the attendance of the scheduling meetings monitored and reported to the maintenance manager?
c. Is the Scheduler providing a detailed list or some tabular or graphical representation of any parts issues that may be present and affect the successful completion of the schedule prior to the scheduling meetings?
12. Scheduling Limits
a. Is there a cap on the amount of resource hours that can happen within a certain area of your business for safety or security reasons?
i. If so, does the scheduling process review that limit?
ii. Does the approved schedule always comply with that limit?
13. Managing changes to schedule resources
a. If there are changes to the available resources that relate to the next scheduling period that is currently being reviewed prior to approval, is there an automated process of notifying all scheduling meeting attendees?
b. If not:
i. Is the scheduler automatically notified?
ii. How long would it be once this change is made before the Scheduler is manually notified?
iii. There is an assumption at this point that the Scheduler would then advise all scheduling meeting attendees of this change.
14. Statutory and Regulatory Work on the schedule
a. When tasks relating to Statute Law or Government Regulations are due and appear on the schedule, is there a clear designation of the significance/importance of that task?
b. If a task relating to Statute Law or Government Regulations is required to be deferred beyond the originally scheduled date (as reviewed in the scheduling meeting), is there a significant process that then takes place to approve or deny that deferral? If the deferral is approved, are the regulators informed within 24hrs?
15. Managing materials associated with the schedule
a. Is there a constant flow of spare parts related information between the scheduler, warehouse and the purchasing officers?
b. If spare parts are not going to be available to the maintainers at least a week prior to the execution dates of the maintenance work, then there is no opportunity for examining the quality or functionality of those parts.
c. Either a quality assurance officer or a maintainer should be allowed sufficient time, suitably prior to the maintenance execution window to examine all parts in detail and then provide this feedback to the scheduler.
[…] article is intended to be read directly following Maintenance Systems Audit Part 1 (Master Data, Maintenance Strategy, Identify, Plan & Schedule […]
[…] Maintenance Systems Audit Part 1 (Master Data, Maintenance Strategy, Identify, Plan & Schedule Work) […]
[…] Maintenance Systems Audit Part 1 (Master Data, Maintenance Strategy, Identify, Plan & Schedule Work) […]