Plan & Schedule
Effective Planning & Scheduling Of Work
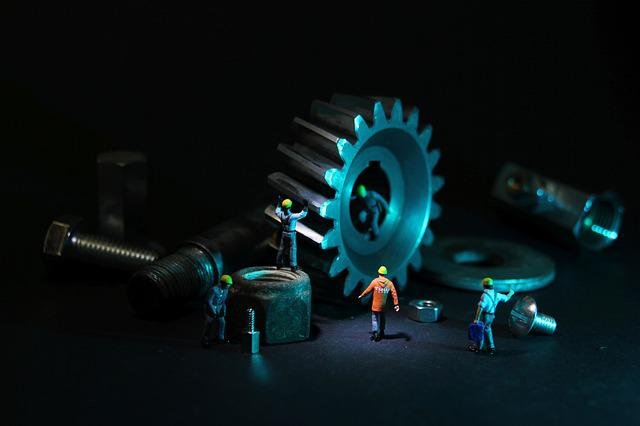
Planning & Scheduling are components of a Work Management Process.
Work Management ensures that maintenance-related tasks are carried out securely in order to keep your business running and to achieve the optimal cost-risk balance for each asset. Thoroughly trained and authorised maintainers complete maintenance work from an approved schedule of fully planned jobs. These tasks need to b e executed completely and in accordance with the standards.
When machinery breakdowns occur, they undoubtedly will put a strain on your best-laid plans but hard work in implementing quality preventative maintenance strategies should reduce equipment failures to a minimum. When creating your strategy-based work, consider the larger business repercussions of potential failures and search for opportunities to conduct this work inside the boundaries of a planned outage event.
Work management serves as the intelligence interface
between the departments of production and maintenance. When teams have access
to quality processes, procedures, training, and experienced maintenance
supervisors, they can operate more safely, effectively, and efficiently. When
compared to unplanned breakdown work, the risks of planned maintenance work are
significantly lower. Specifically, your CMMS work orders enable your
maintenance planners to create a solid planning structure.
Reliability Engineers work very hard to avoid the need
for emergency and break-in work, and they rely heavily on feedback from trades
people during these times. Furthermore, many hours are spent attempting to
increase “Tool Time” and reduce waste by making job duties more
efficient.
Initiate > Plan > Schedule
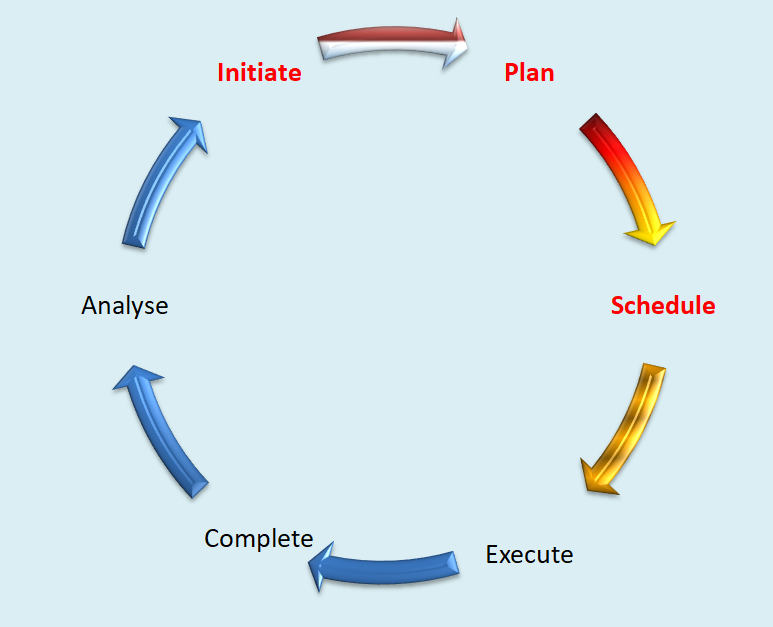
Initiate
The initiate
stage is where your company will aggregate all known maintenance requirements
into a single place. Ensuring quality
in this space by reviewing and approving new work minimises waste in the
planning efforts and will avoid duplication.
Here, your organisation must evaluate all aspects of how to locate
records, classify, and prioritise duties required to maintain asset health.
Inspections and observations, condition monitoring activities, preventative and
predictive maintenance tactics, and other improvement work are just a few
examples of locations where work will be discovered.
Work will
be initiated by a work request or notification, depending on your CMMS and
there should be an established procedure for your company’s expectations for
initiating work.
In an
ideal world, the initiator would be able to assign a risk score to their
request. Initiators must raise their requests at the correct asset level; quite
often, multiple users will create requests for the same problem at different
asset levels, and those charged with reviewing and approving new work cannot be
expected to remember every work request they engage with; these will fall
through the cracks, causing planners to spend a significant amount of time
cleaning up this data.
All new
work requests should be evaluated and authorised once a day in a meeting by at
least two individuals. Work requests should include adequate detail, and if
they don’t, they should be rejected, comments added, and the CMMS should route
this work request back to the initiator. Prior to approval, there should be
only one problem per work request and a risk-based approach for deciding the
final priority of the job.
Plan
Maintenance planning includes determining the scope of work required, challenging the priority of this work, estimating labour requirements and equipment downtime duration. All materials are to be identified and procured, all standard and special tooling listed, support equipment required, and skills needed. The work will need to be scoped and then work instructions created, including management of safety or environmental risks. Tasks are to be consolidated and logically sequenced and work packages created for each sequence.
Maintenance tasks should only be planned once as long as the
Planner applies adequate quality to Work Orders. Review criteria must be
followed when reviewing planned work orders before incorporating them into
upcoming schedules and any work orders coded as “planned” that do not
meet the quality criteria must be rejected, comments added, and your CMMS
should route this work order back to the planner for re-planning.
Schedule
When you have
a quality scheduling process in place, you review the quality of all work
orders coded as fully planned and the approved list of fully planned work
orders will ensure your ability to optimise future production and maintenance
activities and maximise your company’s ability to be cost effective.
Production
requirements, sales commitments, available labour resources, the availability
of materials, tools, and support equipment must all be considered during the
scheduling process. The goal is to create a timetable that minimises the impact
on production while ensuring that maintenance work is completed in an efficient
and cost-effective way.
The schedule build process should be thoroughly documented and approved by all stakeholders. Meetings must be scheduled with adequate time allocated and attendance should be mandatory. Personnel from maintenance, operations, stores, and contractors should be included as stakeholders, and they should actively participate to the formulation of the schedule. Labour estimates should be extended out at least three months to encourage scheduling approved planned work orders as far out into the future as feasible, rather than just next week.
To
optimise downtime and resources, work should be grouped/bundled into the physical
locations that will be affected. To ensure awareness of upcoming work, the
approved schedule should be distributed to all employees. Any statutory or
regulatory work in the schedule should be distinguished from routine
maintenance task to emphasise the significance of this work.
Maintenance Planning & Scheduling
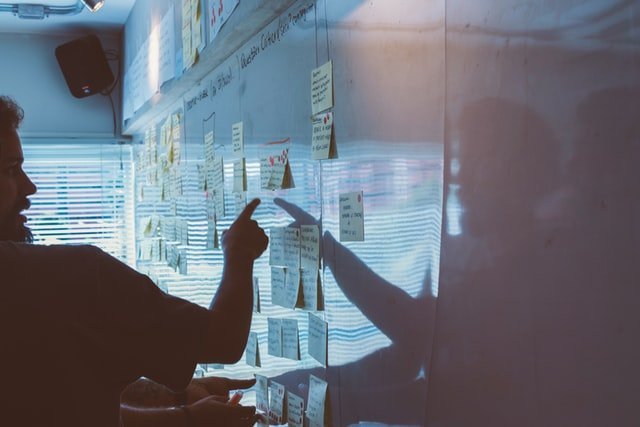
The main duty of the members of the Planning and Scheduling Team is to make sure that business strategies are converted into
formats that can be implemented in the workplace effectively and efficiently, enabling smooth operations, asset utilisation, maintaining your right to
operate, and of course, ‘making money’.
Quality processes are required to ensure that Work Orders are planned and scheduled to the highest standard possible and completed
within the allowed execution windows.
The maintenance department is responsible for ensuring effective asset management system usage through the creation of high-quality work orders and planning processes. To have the greatest influence on all tasks that are related to execution in your operation, all tasks must be scheduled using work orders and relevant business procedures.
Plan a work order within the CMMS

The maintenance work that needs to be done is determined by planning a work order.
This includes determining the scope of the work that needs to be done, assigning an initial priority to this work, estimating labour costs and equipment downtime, identifying the materials, tooling, equipment, and skills that are required, developing work instructions, including management of safety or environmental risks, and grouping tasks into logically sequenced work packages.
In order to maximise the long-term value creation from an asset, we prepare an approved list of completely planned work orders with the goal of optimising future production and maintenance activities. It requires taking into account the need for production, sales obligations, the labour force that is available, materials, tools, and equipment. The goal is to create a timetable that minimises the impact on production while ensuring that the necessary maintenance work is completed effectively and affordably.
Before a work order can be said to be fully planned, the scope of the work must be evaluated.
The work should be broken down into a number of phases or tasks that define the logical steps in the order that they would typically be executed, such as Pre-work Preparation, Work Execution, and Post-work Execution. To guarantee that the work can be completed safely, effectively, and to the desired degree of quality, sufficient detail must be given in the task description. The necessary information and needs are provided using the specifics for each phase. Along with fundamental trade skills, each phase should specify the parts that need to be worked on, the results that are expected, and the precise procedures that will be applied.
When a task involves diagrams, data tables, or images or has a high level of complexity, a technical instruction should be included to the work order. Where one is utilised, a link to the attached document should be included in the job detail. All trade types, materials, services, and tools, in particular specialised tools necessary for carrying out the work must be identified and included in the work order. Where appropriate all this information should be identified at task level. Individual task durations should be evaluated as part of the formulation of the work plan in order to help determine an accurate estimate for the duration of the entire job. All hold points, quality assurance checks, critical measurements, and so on must be properly identified in the work order tasks, and any inspection and testing methods must be included.
When Planned Work Cannot Be Completed
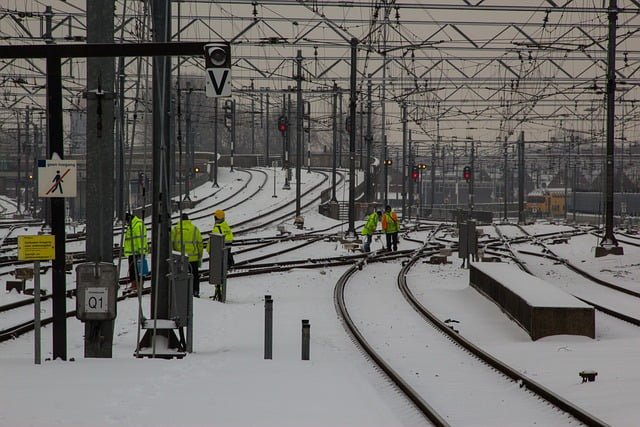
The Maintenance Supervisor should highlight the hazards involved with rescheduling maintenance work, which should then be reviewed and approved by the Maintenance Superintendent.
This rescheduled work’s criticality ranking will determine how far into the future it will appear. Because postponing work is disruptive and sometimes potentially hazardous, you should make rescheduling task stand out by coding these jobs with HSEC and business implications.This data should be regularly analysed by reliability engineers and in some situations avoiding rescheduling a specific task is just as critical to a firm as responding swiftly to an equipment breakdown.
Production Planning & Scheduling

Your company should consider creating an operational plan that includes all plant metrics into a model that replicates plant operation in addition to a comprehensive maintenance management plan. A production profile must be created in order to compare performance against predetermined goals such as Budget versus Expectation. This makes it possible to optimise stakeholder benefit by adjusting a production strategy for the review period.
You must create one prognostic operating plan by combining all production, routine maintenance, and major outage planning activities when creating your operating plan for each period.
The Maintenance & Production Departments must be coordinated; look as far into the future as is practical, with as much accuracy as is manageable and work together to create an effective operating plan. This will give your company a single stream of verified information that can be used to demonstrate your future business intentions & capacities.
Operations may be impacted by both internal and external influences and how well you can coordinate and manage these aspects will determine how successfully you can plan and carry out crucial business tasks like upcoming planned outages.
Production and maintenance personnel carefully analyse your vital data to create future strategies and plans that specify the critical actions and events that must happen. It is crucial that these two plans merge into a single, approved operating plan.
This will give your company agreed-upon and approved critical data that can be entered into the production model and allow for precise forecasting, precise reporting, the provision of key performance information to stakeholders, and the establishment of a timeline for carrying out future actions.
There will inevitably be moments when we have to stop producing in order to accommodate scheduled events. There are a number of causes for this, therefore it’s crucial to consider all of your options in order to minimise the impact outage events may have on your costs per unit of throughput. Your operating plan is the finest tool you will have to present this information, so it is crucial that you understand and are aware of the business demands.
Your operational plan will only be as effective as the information you offer, which is why it is increasingly important to plan and carry out future outage situations with more accuracy and effectiveness.
Not all outages affect the entire operation, and you will frequently be able to stop production in one or more parts of the plant without significantly affecting our capacity to produce, provided that the length of these events does not go beyond a certain point and that the shutting down of the affected parts can be done in a planned manner.
All departments must all be open and honest with one another when it comes to this information if you are ever going to be able to fully understand the significance of the crucial choices made about the functioning of the plant. Your capacity to precisely identify and clearly comprehend the effects of any potential future occurrences and how they can impede you from meeting your production requirements will determine how accurate your long-term planning will be. The priority of any activities you develop in response will be determined by this.
Contact Us.
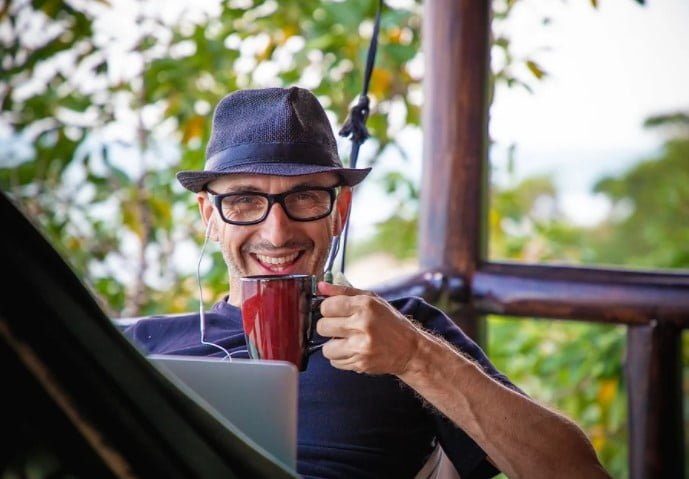
We're Ready, Let's Talk.
Contact Info
Address
PO Box 784, Muswellbrook, NSW, Australia
Email Us
admin@cmmssuccess.com
Call Us
0448 687 451